Welcome to the CASTIpedia
Watch this space for more exciting information coming soon!
CASTI will begin to share our vast collection of technical information in the form of CASTIpedia articles.
Chronological List of CASTIpedia Articles:
What is Carbon Steel? Vol. 2 Chemical Composition - March 8, 2022
What is Carbon Steel? Vol. 1 - March 7, 2022
ASTM Standards: Carbon and Alloy Steels - March 4, 2022
Uncommon Failure in Refinery Tower Collapse - August 9, 2019
How Technical Professionals can Improve Job Prospects as Oil Recovers - January 6, 2017
Temper Bead Welding - October 5, 2016
Benefits of Training - June 17, 2016
Temperature Range Terminology in ASTM and ASME - January 5, 2016
What is Carbon Steel? Vol. 2 Chemical Composition
March 8, 2022 - John E. Bringas
(This article is an excerpt from the ASTM Standards: Carbon and Alloy Steels training course)
Chemical Composition of Carbon Steel
ASTM Standard Chemical Composition Requirement Values
Compliance of the chemical composition requirements of ASTM carbon steel specifications does not mean that every heat of steel is identical; rather, it simply means that the carbon steel product meets or exceeds the requirements set out by the ASTM specifications.
For example, chemical composition requirements in ASTM carbon steel specifications include:
- minimum values, e.g., % silicon,
- maximum values, e.g., % carbon, and
- minimum-maximum range of values, e.g., % manganese,
as demonstrated in the following Connecting-the-Standards© example.
Connecting-the-Standards©: ASTM A106/A106M, TABLE 1 Chemical Requirements | |||
---|---|---|---|
Composition, % | |||
Grade A | Grade B | Grade C | |
Carbon, max | 0.25A | 0.30B | 0.35C |
Manganese | 0.27–0.93 | 0.29–1.06 | 0.29–1.06 |
Phosphorus, max | 0.035 | 0.035 | 0.035 |
Sulfur, max | 0.035 | 0.035 | 0.035 |
Silicon, min | 0.10 | 0.10 | 0.10 |
Chromium, maxC | 0.40 | 0.40 | 0.40 |
Copper, maxC | 0.40 | 0.40 | 0.40 |
Molybdenum, maxC | 0.15 | 0.15 | 0.15 |
Nickel, maxC | 0.40 | 0.40 | 0.40 |
Vanadium, maxC | 0.08 | 0.08 | 0.08 |
A For each reduction of 0.01 % below the specified carbon maximum, an increase of 0.06 % manganese above the specified maximum will be permitted up to a maximum of 1.35 %. B Unless otherwise specified by the purchaser, for each reduction of 0.01 % below the specified carbon maximum, an increase of 0.06 % manganese above the specified maximum will be permitted up to a maximum of 1.65 %. C These five elements combined shall not exceed 1 %. |
ASTM Standards Provide Technical Data
The third function of an ASTM standard is to provide technical data, not only in a table as illustrated in the previous example, but also equally as important in the footnotes or referenced paragraphs to a table. ASTM A106/A106M, TABLE 1 Chemical Requirements, footnotes A, B, and C provide an ideal Connecting-the-Standards© example of ASTM Standards providing technical data, as follows.
Connecting-the-Standards©: ASTM A106/A106M, TABLE 1 Chemical Requirements | ||||||||||||
---|---|---|---|---|---|---|---|---|---|---|---|---|
Composition, % | ||||||||||||
Grade A | Grade B | Grade C | ||||||||||
Carbon, max | 0.25A | 0.30B | 0.35C | |||||||||
Manganese | 0.27–0.93 | 0.29–1.06 | 0.29–1.06 | |||||||||
Phosphorus, max | 0.035 | 0.035 | 0.035 | |||||||||
Sulfur, max | 0.035 | 0.035 | 0.035 | |||||||||
Silicon, min | 0.10 | 0.10 | 0.10 | |||||||||
Chromium, maxC | 0.40 | 0.40 | 0.40 | |||||||||
Copper, maxC | 0.40 | 0.40 | 0.40 | |||||||||
Molybdenum, maxC | 0.15 | 0.15 | 0.15 | |||||||||
Nickel, maxC | 0.40 | 0.40 | 0.40 | |||||||||
Vanadium, maxC | 0.08 | 0.08 | 0.08 | |||||||||
A For each reduction of 0.01 % below the specified carbon maximum, an increase of 0.06 % manganese above the specified maximum will be permitted up to a maximum of 1.35 %. B Unless otherwise specified by the purchaser, for each reduction of 0.01 % below the specified carbon maximum, an increase of 0.06 % manganese above the specified maximum will be permitted up to a maximum of 1.65 %. C These five elements combined shall not exceed 1 %. Explanation
|
The common carbon steelmaking elements of: carbon (C), manganese (Mn), silicon (Si), aluminum (Al), phosphorus (P), and sulfur (S), residual chemical elements, and unspecified chemical elements, as defined in ASTM A941 and used within ASTM steel standards, will be addressed in the article "What is Carbon Steel? Vol. 3" which is an excerpt from the ASTM Standards: Carbon and Alloy Steels training course.
What is Carbon Steel? Vol. 1
March 7, 2022 - John E. Bringas
(This article is an excerpt from the ASTM Standards: Carbon and Alloy Steels training course)
Carbon steel is commonly considered to be a “mixture of iron and carbon”, along with “other chemical elements” that are part of commercial steelmaking and required to obtain specific properties for the intended applications.
These “other chemical elements” can make commercial carbon steels much more complex than simply a mixture of iron and carbon, as described in the ASTM definition in the following Connecting-the-Standards© example.
Connecting-the-Standards©: ASTM Definition of Carbon Steel |
---|
ASTM A941 Standard Terminology Relating to Steel, Stainless Steel, Related Alloys, and Ferroalloys carbon steel, n—a steel that conforms to a specification that prescribes a maximum limit, by heat analysis in mass percent, of not more than: 2.00 for carbon and 1.65 for manganese, but does not prescribe a minimum limit for chromium, cobalt, molybdenum, nickel, niobium (columbium), tungsten (wolfram), vanadium, or zirconium. DISCUSSION—Except as required above, it is permissible for carbon steel specifications to prescribe limits (minimum or maximum, or both) for each specified alloying element, subject to the following restrictions for the heat analysis limits in mass percent:
|
- Note that this ASTM A941 definition is intended to be applied within ASTM steel specifications, where the term carbon steel is clearly based on 2.00 % carbon and 1.65 % manganese maximum limits by heat analysis in mass percent,
- no prescribe minimum limit for chromium, cobalt, molybdenum, nickel, niobium (columbium), tungsten (wolfram), vanadium, or zirconium; and
- with 6 exceptions noted in the Discussion; for example, wrought and cast products have different maximum limits for silicon content, 0.60% versus 1.00% respectively, that will affect several properties, such as weldability, formability, ductility, etc.
One of the more interesting Discussion exceptions is note (f) that permits ASTM carbon steel specifications to prescribe a copper minimum requirement not to exceed 0.35 mass percent for heat analysis. The addition of a limited amount of copper in carbon steels is commonly for improved atmospheric corrosion resistance, such as for bridge structural steels, as shown in the following Connecting-the-Standards© example.
Connecting-the-Standards©: Copper Addition and Atmospheric Corrosion Resistance |
---|
ASTM A709/A709M Structural Steel for Bridges 13. Atmospheric Corrosion Resistance 13.1 Steels meeting this specification provide three levels of atmospheric corrosion resistance: 13.1.1 Steel grades without suffix provide a level of atmospheric corrosion resistance typical of carbon or alloy steel without copper. 13.1.2 The steel for Grades 50W [345W], HPS 50W [HPS 345W], and HPS 70W [HPS 485W] shall have an atmospheric corrosion resistance index of 6.0 or higher, calculated from the heat analysis in accordance with Guide G101, Predictive Method Based on the Data of Larabee and Coburn (see Note 3). When properly exposed to the atmosphere, these steels can be used bare (unpainted) for many applications. The steel for Grade HPS 100W [HPS 690W] provides an improved level of atmospheric corrosion resistance over alloy steel without copper. 13.1.3 The steel for Grade 50CR [345CR] may be used bare (unpainted) in some applications where traditional weathering steel does not perform successfully. NOTE 3—For methods of estimating the atmospheric corrosion resistance of low-alloy steels, see Guide G101. The user is cautioned that the Guide G101 predictive equation (Predictive Method Based on the Data of Larabee and Coburn) for calculation of an atmospheric corrosion resistance index has only been verified for the composition limits stated in that guide. ASTM A941 Standard Terminology Relating to Steel, Stainless Steel, Related Alloys, and Ferroalloys atmospheric corrosion resistance, n—the ability to resist degradation or alteration of material through chemical reaction with the surrounding atmosphere. DISCUSSION—This term generally pertains to carbon steel, low alloy steel, or micro-alloyed steel. |
In this example, even though there is an intentional minimum addition of copper, provided the minimum specified addition in ASTM A709/A709M is less than 0.35% copper by mass percent in the heat analysis, this material would be classified as a carbon steel in accordance with the ASTM A709/A709M and ASTM A941.
Also, keep in mind that ASTM A709/A709M includes both carbon steels and low-alloy steels, such that the user would need to know where carbon steel stops and where low-alloy steel starts. The ASTM A941 low-alloy steel definition will be covered in another article.
The common steelmaking elements of carbon (C), manganese (Mn), silicon (Si), aluminum (Al), phosphorus (P), and sulfur (S), will be addressed in the article What is Carbon Steel? Vol. 2 which is an excerpt from the ASTM Standards: Carbon and Alloy Steels training course.
ASTM Standards: Carbon and Alloy Steels
March 4, 2022 - John E. Bringas
(This article is an excerpt from the ASTM Standards: Carbon and Alloy Steels training course)
What are ASTM Standards?
The Regulations Governing ASTM Technical Committees, commonly called the "Green Book" since it's front cover is green, are formal rules that are used to develop consensus standards in accordance with rigorous democratic procedures, including voting on each new standard and all changes to existing standards. All ASTM Technical Committee members are volunteers (i.e., they are not paid by ASTM) and do not include ASTM staff personnel. Likewise, an ASTM Standard is achieved through consensus agreement within a committee and cannot be controlled by an individual or small group within the committee, as defined in the following Connecting-the-Standards© example.
Connecting-the-Standards©: ASTM Consensus Standard |
---|
Regulations Governing ASTM Technical Committees consensus, n—the judgment arrived at through the balloting and review procedures of these regulations. DISCUSSION—Specific guidelines for reaching consensus on each type of ballot or motion are provided in the individual voting procedures. standard, n—as used in ASTM International, a document that has been developed and established within the consensus principles of the Society and that meets the approval requirements of ASTM procedures and regulations. DISCUSSION—The term “standard” serves in ASTM International as a nominative adjective in the title of documents, such as test methods or specifications, to connote specified consensus and approval. The various types of standard documents are based on the needs and usages as prescribed by the technical committees of the Society. |
Types of ASTM Standards
In the 2022 Annual Book of ASTM Standards, there are 12,800+ standards—including 961 Steel Standards across 8,896 pages—that are used to assist steel producers, users and purchasers.
There are 5 types of ASTM standards, all of which apply to steels, as follows.
- Standard Specification
- Standard Practice
- Standard Test Method
- Standard Terminology
- Standard Guide
Each of the 5 types of ASTM standards are defined in the Regulations Governing ASTM Technical Committees and as shown in the following Connecting-the-Standards© examples.
1. Standard Specification
An ASTM Standard Specification contains technical information to assist both the purchaser and the supplier through standardization, defined as follows.
Connecting-the-Standards©: ASTM Standard Specification |
---|
specification, n—an explicit set of requirements to be satisfied by a material, product, system, or service. DISCUSSION—Examples of specifications include, but are not limited to, requirements for; physical, mechanical, or chemical properties, and safety, quality, or performance criteria. A specification identifies the test methods for determining whether each of the requirements is satisfied. |
Example: ASTM A1 Standard Specification for Carbon Steel Tee Rails.
2. Standard Test Method
An ASTM Standard Test Method produces a test result, whereas a Standard Practice does not produce a test result, defined in the following Connecting-the-Standards© example.
Connecting-the-Standards©: ASTM Standard Test Method |
---|
test method, n—a definitive procedure that produces a test result. DISCUSSION—Examples of test methods include, but are not limited to: identification, measurement, and evaluation of one or more qualities, characteristics, or properties. A precision and bias statement shall be reported at the end of a test method. |
Example: ASTM E8/E8M Standard Test Methods for Tension Testing of Metallic Materials
3. Standard Practice
An ASTM Standard Practice does not produce a test result, whereas a Standard Test Method does produces a test result, defined in the following Connecting-the-Standards© example.
Connecting-the-Standards©: ASTM Standard Practice |
---|
practice, n—a set of instructions for performing one or more specific operations that does not produce a test result. DISCUSSION—Examples of practices include, but are not limited to: application, assessment, cleaning, collection, decontamination, inspection, installation, preparation, sampling, screening, and training. |
Example: ASTM A275/A275M Standard Practice for Magnetic Particle Examination of Steel Forgings
There are occasions when an ASTM Standard Practice becomes a Test Method as it gets further developed through committee ballot.
4. Standard Terminology
A critical component of standardization is the terminology used to write standards, since without standardized terminology a term may have multiple conflicting definitions that would be able to achieve consensus. Consequently, ASTM Standard Terminology is developed in individual documents within a committee for general application of its terms and definitions, as well as Terminology Sections within ASTM standards where a more specific definition is require for a term used within that standard, defined in the following Connecting-the-Standards© example.
Connecting-the-Standards©: ASTM Standard Terminology |
---|
terminology, n—a document comprising definitions of terms; explanations of symbols, abbreviations, or acronyms. |
Example: ASTM A941 Standard Terminology Relating to Steel, Stainless Steel, Related Alloys, and Ferroalloys
5. Standard Guide
An ASTM Standard Guide is written to provide options to the user, based on the information it provides, defined in the following Connecting-the-Standards© example.
Connecting-the-Standards©: ASTM Standard Guide |
---|
guide, n—a compendium of information or series of options that does not recommend a specific course of action. DISCUSSION—A guide increases the awareness of information and approaches in a given subject area. |
Example: ASTM A700 Standard Guide for Packaging, Marking, and Loading Methods for Steel Products for Shipment.
Functions of ASTM Specifications
ASTM specifications may have three major functions, described in the Form and Style for ASTM Standards as follows:
Form and Style for ASTM Standards
- Purchasing,
- Standardization, and
- Providing Technical Data.
These 3 functions are described in the Form and Style for ASTM Standards, commonly called the "Blue Book" since it's front cover is blue, as shown in the following Connecting-the-Standards© example.
Connecting-the-Standards©: ASTM Specification Functions |
---|
Purchasing Specifications facilitate dealings between the purchaser and the supplier. Sufficient requirements should be included to ensure that all batches, lots, or deliveries from any seller that conform to the specification will be satisfactory to the purchaser. Unnecessary requirements are likely to increase costs and should be avoided. Standardization Standardization is an inevitable byproduct of most specifications. In some cases it may be the primary function. Standardization involves a deliberate and possibly arbitrary choice of a limited number from the multiplicity of qualities, sizes, compositions, etc., that may be available. Providing Technical Data All specifications contain technical information, but in some cases the designer requires more information than that provided for purchase or standardization. Committees may add information of this type to specifications either as requirements or as appendixes. |
Terminology: ASTM Standards, Other Standards, and Nonstandard (Slang)
It is important to understand that all ASTM standard terms may not be identically defined by other standards development organizations (SDO), e.g., API, NACE, ASME, AWS, ASCE, SAE, CEN, JIS, etc., other technical sources, e.g., ASM International, handbooks, etc., regulatory bodies (CSB, PHMSA, NEB, etc.), or corporations.
Many of the differences in terms and definitions published by SDOs and non-SDOs can be explained by the fact that SDO standards are peer reviewed and consensus based by democratic voting procedures within industry-wide committees. Whereas non-SDOs, e.g., some technical societies, regulatory bodies, corporations, etc., publish terms and definitions that are not commonly peer reviewed and are not consensus based with input from individuals outside of their organization, and in some cases can be written by an individual person. These terminology differences often make technical understanding to be very confusing and difficult, but the very fact that the same term can have multiple definitions depending on the authoring body is critical to understanding how the term should be appropriately used. These various definitions are generally similar but can vary in important details.
“Nonstandard” terms and definitions become even more confusing and difficult to understand and appropriately use because they may be considered to be “slang” or “shop talk” where the term may not even have a written definition, e.g., “that’s what I was always told the term meant, but I was never told its source”
ASTM standard terminology is a fundamentally important concept to understanding all ASTM standards, including: product specifications, test methods, and practices. From time-to-time, nonstandard terms, slang, or shop talk will be introduced so that you are aware of the differences and the issues that can arise as compared to using ASTM standard terms.
Most ASTM steel specifications contain a Terminology section with terms and definitions specific to it, as well as there are 8 standalone ASTM Terminology Standards, demonstrated as follows
"Terms and Definitions Specific to a Standard" is the first type of ASTM Standard Terminology. These terms are contained in a Terminology Section within the standard, meaning they were not written to be used outside of this standard.
For example, ASTM A131 Structural Steel for Ships, Section 3, Terminology includes the term: control rolling as used within ASTM A131 and not specifically written to used in other ASTM steel standards, as shown in the following Connecting-the-Standards© example.
Connecting-the-Standards©: ASTM Standard Terminology |
---|
ASTM A131/A131M Standard Specification for Structural Steel for Ships 3. Terminology 3.1 Definitions of Terms Specific to This Standard: 3.1.1 control rolling (controlled rolling), n—a hot deformation process intended to provide austenite (and hence ferrite) grain refinement by careful control of the pass-by-pass temperature/reduction schedule at high temperature regime... |
The second type of ASTM Standard Terminology is a "General Terminology Standard", which are commonly referenced within an ASTM specification, test method, or practice that are applied for terms contained within them, that are not included in the terms “Terms and Definitions Specific to a Standard”.
For example, ASTM A6, paragraph 3.2 references the "General Terminology Standard" ASTM A941, as shown in the following Connecting-the-Standards© example.
Connecting-the-Standards©: ASTM Standard Terminology |
---|
ASTM A6/A6M General Requirements for Rolled Structural Steel Bars, Plates, Shapes, and Sheet Piling 3. Terminology 3.2 Refer to Terminology A941 for additional definitions of terms used in this standard. |
The following list contains 8 standalone ASTM Terminology Standards applicable to steels and cast irons.
ASTM General Terminology Standards for Steels and Cast Irons
- ASTM A644 Standard Terminology Relating to Iron Castings
- ASTM A902 Standard Terminology Relating to Metallic Coated Steel Products
- ASTM A941 Standard Terminology Relating to Steel, Stainless Steel, Related Alloys, and Ferroalloys
- ASTM F547 Standard Terminology of Nails for Use with Wood and Wood-Base Materials
- ASTM F552 Standard Terminology Relating to Chain Link Fencing
- ASTM F1379 Standard Terminology Relating to Barbed Tape
- ASTM F1789 Standard Terminology for F16 Mechanical Fasteners
Uncommon Failure in Refinery Tower Collapse
August 9, 2019 - John E. Bringas
The Failure
When the aviation fuel processing tower collapsed on April 2, 2019 at the Imperial Oil refinery in Sarnia, Ontario, it was very fortunate that no one was injured and no releases to air or water occurred. To Imperial Oil’s credit, on June 6, 2019, they posted a message on their Facebook page explaining why the tower collapsed.
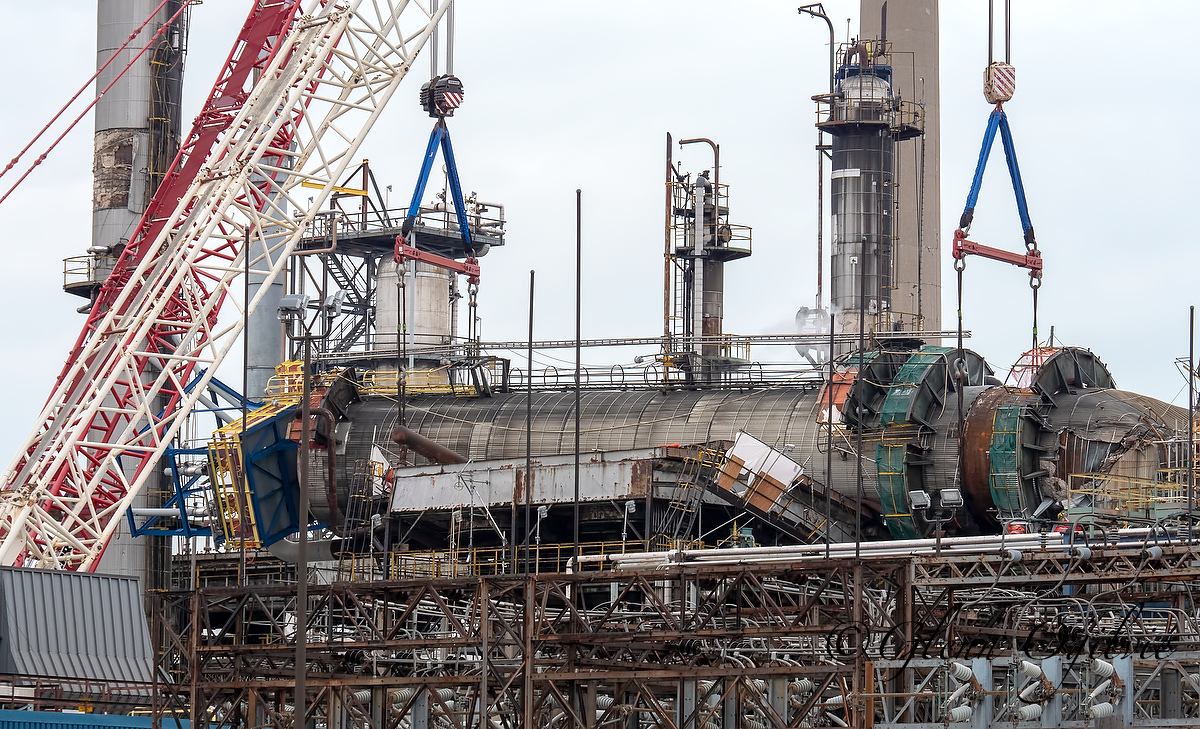
In short, this posting mentioned that: “The Imperial Oil investigation identified that a design change made to the tower during the last maintenance period had unknowingly increased the risk of pyrophorics.” Consequently, the probability and consequences of pyrophoric materials developing from operation and leading to a failure during a shutdown period were not sufficiently established in the design change.
When the tower was opened for inspection, it allowed the ambient air (oxygen) to enter the tower which caused the pyrophoric materials that had unknowingly built-up during operation to auto-ignite, producing high temperatures that the tower was not designed to support and the tower collapsed.
Because this failure mechanism does not occur during operation, as most do, it falls into a unique category of “shutdown” mechanisms, which for example, also includes polythionic stress corrosion cracking.
There were many news reports of the failure, although the The Sarnia Journal news report included the photo of the collapsed tower shown above.
Learning More About the Pyrophoric Damage Mechanism
The potential of pyrophoric material related failure in refinery equipment is well-known and commonly addressed with good engineering design practices. Likewise, these types of failures are not common. In fact, after 41 years of engineering and inspection experience, I have never seen this type of failure, so I wanted to learn more about it and started researching the literature.
Having taught a course covering API RP 571 Damage Mechanisms Affecting Fixed Equipment in the Refining Industry since the first edition in 2003, I knew that pyrophoric material damage was not addressed in it. So my next step was to review API 579-1/ASME FFS-1 Fitness-For-Service standard where pyrophoric material damage is not specifically addressed and is only briefly mentioned in 9.5.2.2 d) with a reference to hazardous materials with auto-ignition temperatures.
My next step was to review API RP 580 Risk-based Inspection, however, pyrophoric material damage is also not covered in it.
Going down my check list, I went to API RP 581 Risk-based Inspection Methodology and jackpot! I was pleasantly surprised to find references to pyrophoric materials and auto-ignition temperatures. For example, 4.8.6 establishes the consequence area calculations that yield significantly different results depending on whether the auto-ignition “not likely consequence” equations are used or “auto-ignition likely consequence” area equations are used.
We will certainly include this case study in the API RP 571 and ASME Codes Damage Mechanisms course offered by Codes and Standards Training Institute (CASTI), along with many other case studies of damage mechanisms.
How Technical Professionals can Improve Job Prospects as Oil Recovers
January 6, 2017 - Patrick Law
News of OPEC and other oil-producing countries cutting oil output to raise oil prices has provided optimism to the oil and gas industry, but employers are still cautious when it comes to increasing operations and hiring technical professionals. Companies are positioning themselves to be flexible enough to ramp up operations quickly while also being able to cut costs if the oil downturn continues, and for that, they need a certain type of person.
The oil and gas industry is regulated so that many positions require certified individuals. Companies need flexible employees who can fulfill multiple roles. Many engineers, for example, perform both engineering and inspection duties. Similarly, many welders are certified to undertake welding inspection. Someone with multiple certifications is a very valuable asset to a company.
Obtaining certifications is an obvious choice, but the difficulty is in deciding which ones best supplement existing credentials. Codes and Standards Training Institute (CASTI) provides a detailed career path diagram that will assist you by showing the certifications that can help you keep or obtain a job. Engineers, welders, and inspectors all benefit from certifications.
When employers look for flexible employees, engineers that can perform inspection have a clear advantage. CASTI provides training for many different types of inspection certification examinations including welding inspector certification and American Petroleum Institute (API) inspector certification. It is valuable for engineers to obtain at least one American Petroleum Institute (API) inspector certification, giving employers more flexibility to send them out to the field. API 510, 570, and 653 inspector certifications allow individuals to inspect pressure vessels, piping, and storage tanks respectively; all of which are abundant in the oil and gas industry.
A welder that is certified to inspect welds, pressure vessels, piping, and storage tanks is a valuable asset in a broad range of industrial applications. Welders should start with a welding inspector certification. In qualification as a welding inspector, code endorsement examinations are required which permit the inspection of specific types of equipment. The more code endorsements that a welding inspector has, the more versatile they are.
Certified inspectors should continue to broaden the types of equipment that they can inspect. Oil and gas companies have a lot of equipment to inspect, and they prefer to hire one inspector instead of three or four. The ability to inspect multiple types of equipment is especially useful for performing inspection work for larger companies that may have pressure vessels, piping, and storage tanks on site.
Improving your job prospects in the oil and gas industry requires effort, but if you are able to obtain several certifications, you will be of great value to employers. Sign up for the CASTI e-newsletter to receive information on training courses for specific certifications and notifications of when new online-only courses will be available.
Temper Bead Welding
October 5, 2016 - Patrick Law
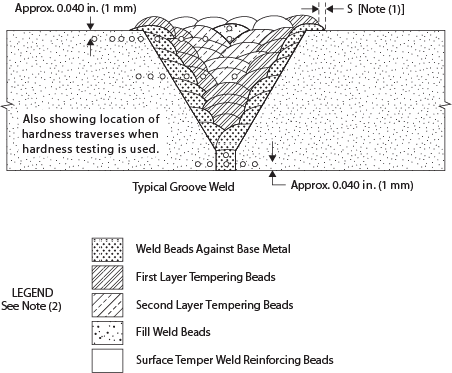
Nomenclature for Temper Bead Welding
On September 28, 2016, Kimberley Meszaros of CASTI gave a presentation to the CWA Calgary chapter entitled "Connecting-the-Codes from Temper Bead Welding to the ASME Codes, CSA Codes, and the NBIC." Due to popular demand, we have now made the presentation slides available for download here.
Temper Bead Welding (TBW) was adopted into the 2004 Edition of the ASME Boiler and Pressure Vessel Code, Section IX; the adoption of TBW has permitted welders to strategically exploit the effects of welding. Of particular note, is the ability to utilize TBW to create a weldment with improved strength and low temperature impact properties without the application of post weld heat treatment (PWHT). However, to reliably obtain these benefits requires development of a robust welding procedure, performance qualification and parameter controls during production welding.
ASME Section IX, QW-290, describes the rules for TBW procedure qualification, upgrading of existing procedures to include TBW, restrictions on the use of TBW, qualification of welders and variables for TBW, among other topics. The rules for TBW in Section IX and a selection of other codes will be discussed.
Kimberley Meszaros, (P.Eng, MSc) is a professional engineer who practices materials engineering. She is a certified welding inspector. Kimberley is a BSc (Materials Engineering) and MSc (Materials Engineering-Welded Composite Coatings for Oil Sands) graduate of the University of Alberta. Kimberley has worked in the Alberta energy sector developing and troubleshooting welding procedures, consulting on various projects, and has worked in research and development for both private and government organizations.
Benefits of Training
June 17, 2016 - Katie Cheung
Invest in Your Career
Your education is like a business investment. It takes time and money to complete training courses and obtain certification, but you will see an excellent return on an investment that will continue to give back throughout your entire career.
Enhance Your Skills
It is important to ensure that your knowledge and skills are up-to-date with the trends affecting your industry so employers will continue to view you as a valuable asset to the company. By continuing your education, you can learn new skills and specializations that will allow you to become a more versatile employee and increase your long-term value to employers.
Demonstrate Value to Employers
An excellent way to demonstrate to employers that you are committed to your career is by attending training courses. By investing time and money in continuing your education, you will send a powerful message to employers that you are serious about improving your education and applying new skills to your job. Employers are more likely to hire and retain professionals who show the desire and commitment for lifelong learning, and many even provide tuition reimbursement as added encouragement.
Leverage Past Experience
Earning additional credentials will attest to your capability and is also a good source of knowledge and networking. It will significantly improve your marketability and the more certifications obtained the better likelihood of achieving the supervisor or managerial levels.
Discover Your Dream Job
From welder to inspector, the best way to learn more about a potential career in supervisory and managerial positions is through training and certification. By continuing your education, you can discover a dream job that is less physically demanding and increases your earning potential.
Increase Your Earning Potential
If you are looking to achieve a higher salary over the life of your career: get the training you need to get ahead. Get where you want to be by knowing where you need to be. Get on the CASTI Career Path today.
Temperature Range Terminology in ASTM and ASME
January 5, 2016 - John E. Bringas
Question:
In ASTM and ASME Section II, there are terms used to describe service temperature, such as:
- cryogenic (ASME SA-353),
- low temperature (ASME SA-333),
- moderate temperature (ASME SA-516), and
- elevated temperature (ASME SA-387).
The temperature ranges for these terms are not included in ASTM A941; where would I be able to find them?
Answer:
The answer to this question is found in ASTM A994 as shown below.
ASTM A994 Standard Guide for Editorial Procedures and Form of Product Specifications for Steel, Stainless Steel, and Related Alloys
6.1.5 The use of temperature categories in the titles of specifications should be avoided. When a subcommittee determines that temperature categories must be used in the title of a specific standard, numerical temperature ranges should not be used; the establishment of limits on the use of materials is not the responsibility of Committee A01. When a subcommittee determines that a temperature category must be used in a title, one of the following should be selected: cryogenic, low, ambient, moderate, elevated, or high.
There are no quantitative values established by ASTM for any of the temperature descriptions in the standard title since only the user of the ASTM standard knows the temperature values for their application.
For example, although ASTM A106 includes the term "high temperature" in its title, this standard is used in many industries and is included in many construction codes where "high temperature" could have many different temperatures or ranges.
In the case of ASME B31.3, ASTM A106 Grade B has a listed allowable stress from the design minimum temperature up to 593°C. The Category D design minimum temperature without impact testing for ASTM A106 can be as low as -29°C. Therefore, the ASME B31.3 code includes a -29°C to 593°C temperature range for ASTM A106 Grade B that ASTM classifies as "high temperature".
If you did this same exercise for other codes, e.g., water treatment, structural, plumbing, natural gas distribution, etc., you will find many different allowable temperature ranges for ASTM A106. Consequently, it's the user's responsibility to understand their application and its material selection requirements.
Copyright
© 2022 Codes and Standards Training Institute (CASTI) Inc. All rights reserved. All CASTI website content and training materials are the property of CASTI and protected under Canadian and International copyright laws. Use of any CASTI content without written permission from CASTI is illegal. No part of CASTI content may be reused, reproduced, or redistributed in any form or by any means—graphic, electronic, or mechanical, including photocopying, recording, taping, information storage, or retrieval systems—without the written permission of CASTI. CASTI reserves the right to revise these policies, terms, and conditions at any time without notice.
Disclaimer
The information on this website is provided as a public service for information purposes only; it is not engineering or consulting advice and should not be relied upon in such a manner. While the information on this website is thought to be accurate, it is provided on an “as is” basis and without warranty of any kind, either express or implied. Codes and Standards Training Institute (CASTI), its agents, employees or contractors will not be liable to you for any loss or damages of any nature arising out of your use of information provided on this website, or information provided at any other website that can be accessed from this website.